Customer Success Story
With Industry 4.0 monitoring solution from Schaeffler
The maintenance management function of long-established Polish company Albeco uses the digital monitoring solution Schaeffler OPTIME to simplify and accelerate its daily service operations. The company uses the OPTIME app to assist in this process, which enables customer data to be created and managed with minimal effort. This establishes a knowledge advantage which does not require on-site presence, allowing the responsible maintenance personnel to act swiftly in making the right decisions. And the value of this digital solution: Simply unbeatable.
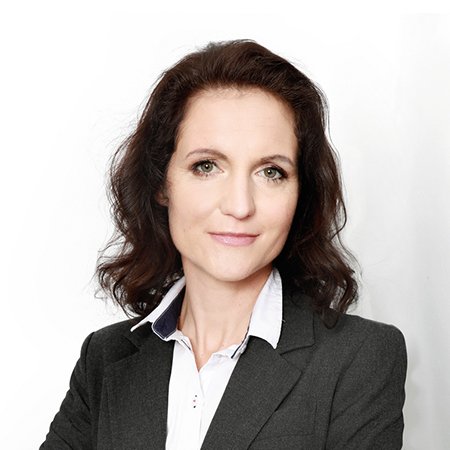
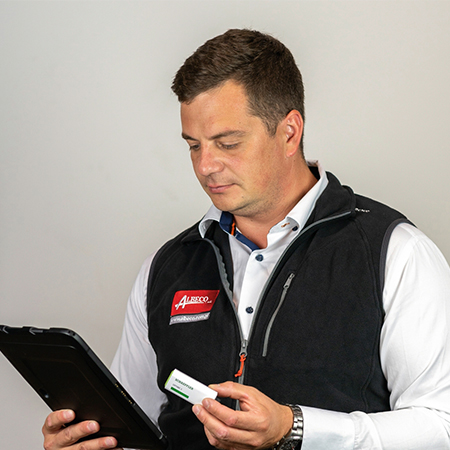
Benefits
All customer data available at a glance with just one app
Reduced travel to the customer thanks to digital data management
More efficient planning of maintenance measures, staff, and replacement part procurement
Increased customer satisfaction thanks to greater security and good conditions
Challenge
“The greatest challenge lies in dispelling the misperception that machine diagnosis is not required. Presenting a convincing case to customers on the benefits of predictive maintenance is a top priority for us,”
states Jakub Burdajewicz, Service Expert for Condition Monitoring
“The technical challenge lies in monitoring the multitude of machines involved in complex production processes. Managing the vast amount of customer data and minimizing on-site visits to customer sites are of the essence here,”
he continues.
Albeco sought assistance on this matter from preferred partner Schaeffler.
Solution
What's special
The sensors monitor the machinery and equipment at the customer’s site. The gateway receives the data from the sensors and transfers these to the Schaeffler cloud. OPTIME detects problems, alarms accordingly and provides information about the possible cause of the problem. Expert knowledge of condition monitoring is not required as this knowledge is already integrated in OPTIME in the form of Schaeffler know-how.
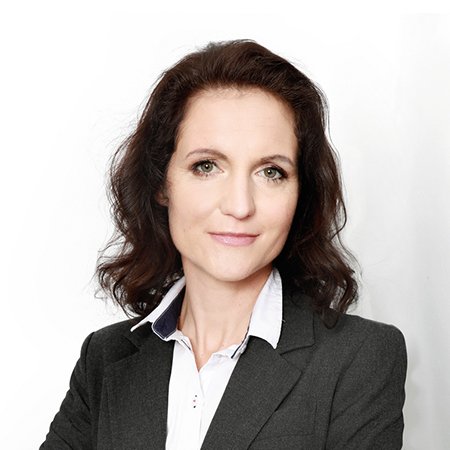