Table of contents
Axial spherical roller bearings
- Load carrying capacity
- Compensation of angular misalignments
- Lubrication
- Sealing
- Speeds
- Noise
- Temperature range
- Cages
- Internal clearance
- Dimensions, tolerances
- Suffixes
- Structure of bearing designation
- Dimensioning
- Minimum load
- Design of bearing arrangements
- Mounting and dismounting
- Legal notice regarding data freshness
- Further information
Axial spherical roller bearings
Axial spherical roller bearings are suitable where:
- bearing arrangements are subjected to high and very high axial loads ➤ section
- dynamic or static misalignments of the shaft relative to the housing, or deflections of the shaft, must be compensated by the bearing under axial loads ➤ section
- radial forces occur in addition to axial forces (maximum 55% of Fa ) ➤ section
- a relatively high speed suitability is required in addition to a high load carrying capacity ➤ section
- high shock type loads must be supported
- bearing parts are to be mounted separately (the bearings are not self‑retaining) ➤ section
Axial spherical roller bearing: comparison of load carrying capacity with axial deep groove ball bearing, compensation of misalignments Fa = axial load Ca = basic axial dynamic load rating |
![]() |
Bearing design
Design variants
Axial spherical roller bearings are available in the basic design as:
- an increased capacity design with sheet steel cage or solid brass cage ➤ Figure
X-life bearings
The bearings are available in the majority of sizes as X-life bearings ➤ Figure
The bearing design is dependent on the bearing series and the bearing size. It essentially differs in the configuration and guidance of the cage ➤ section.
Bearings of basic design
The raceway in the housing locating washer has a curved form
Axial spherical roller bearings are part of the group of axial roller bearings. These single row, non-self-retaining rolling bearings comprise solid shaft and housing locating washers with raceways for the rolling elements. Cages guide the large number of asymmetrical barrel rollers ➤ section. The cage, roller and cage assembly, and shaft locating washer form a self-retaining unit. The raceways are arranged oblique to the bearing axis, the raceway in the housing locating washer is of a concave design. This design allows these bearings to combine a range of characteristics, which are essential to many applications, in one bearing, such as angular adjustability for example ➤ section.
Roller contact design
The stress distribution at the contact points between the rollers and raceways is determined by the contact surface of the rollers. As a result, the roller geometry is matched to the raceway. This gives a favourable load distribution over the entire length of the roller and thus prevents both edge stresses and stress peaks at the ends of the roller.
Increased capacity design with sheet steel cage or solid brass cage
Bearings with sheet steel cage
Bearings without a cage suffix have coated sheet steel cages, which are guided by rollers ➤ Figure and ➤ section. These designs are available as X-life bearings ➤ link.
Bearings with solid brass cage
Bearings with the cage suffix MB have solid brass cages that are guided on the shaft locating washer or by the rollers ➤ Figure and ➤ section. The MB design is also available in numerous sizes as X-life bearings ➤ link.
Axial spherical roller bearings of basic design Fr = radial load Fa = axial load
|
![]() |
X-life premium quality
X-life bearings exhibit considerably higher performance than conventional axial spherical roller bearings. This is achieved, for example, through the modified internal construction, the optimised contact geometry between the rollers and raceways, the new cage design, a higher steel quality, better surface quality and optimised roller guidance and lubricant film formation.
Axial spherical roller bearing in X-life design
|
![]() |
Advantages
Increased customer benefits due to X-life
These technical enhancements offer a range of advantages, such as:
- a more favourable load distribution in the bearing and thus a higher dynamic load carrying capacity of the bearings
- downsizing possible, increased performance density
- a higher fatigue limit load
- a higher running accuracy and smooth running
- running with reduced friction and greater energy efficiency
- lower heat generation in the bearing
- higher possible speeds
- lower lubricant consumption and therefore longer maintenance intervals if relubrication is carried out
- a measurably longer operating life of the bearings
- high operational security
- compact, environmentally-friendly bearing arrangements
Lower operating costs, higher machine availability
In conclusion, these advantages improve the overall cost-efficiency of the bearing position significantly and thus bring about a sustainable increase in the efficiency of the machine and equipment.
Suffix XL
X-life axial spherical roller bearings include the suffix XL in the designation ➤ section and ➤ dimension table.
Areas of application
Wide application range
Due to their special technical features, X-life axial spherical roller bearings are highly suitable for bearing arrangements in:
- refiners and worm extruders in the pulp and paper industry
- drilling rigs and roll pressers in the cement industry, mining and raw material processing
- work rolls and back-up rolls in cold rolling mills
- extruder gearboxes in chemical plant and refineries
- air preheaters in thermal power stations
- POD and azimuth drives in marine propulsion systems
X-life indicates a high product performance density and thus a particularly significant benefit to the customer. Further information on X-life ➤ link.
Load carrying capacity
Designed for very high axial loads and high radial loads
Axial spherical roller bearings can support very high axial loads in one direction and – since the raceways are inclined relative to the bearing axis – radial loads acting simultaneously. They are designed for very high load carrying capacity and, since they have the maximum possible number of large and long barrel rollers, are also suitable for the heaviest loads. As a result of the inclined raceways, the load is transmitted from one raceway to the other oblique to the bearing axis ➤ Figure. Due to the optimised osculation conditions between the rollers and raceways, uniform stress distribution is achieved in the bearing.
The radial load (Fr, F0r) must not exceed 55% of the axial load ➤ Equation and ➤ Equation.
Force flow under axial load The load is transmitted from one raceway to the other oblique to the bearing axis. |
![]() |
Compensation of angular misalignments
Axial spherical roller bearings compensate dynamic and static angular misalignments
Due to the concave rolling element raceway in the housing locating washer, axial spherical roller bearings are capable of angular adjustment. As a result, they permit skewing between the shaft locating washer and housing locating washer within certain limits, without causing damage to the bearings or impairing their function. In this way, they can compensate misalignment, shaft deflection and housing deformation ➤ Table. The extent to which these table values can be used in practice is, however, essentially dependent on the design of the bearing arrangement, the type of seal and other factors.
Permissible adjustment angle
The adjustment angles given in the table are permissible under the following conditions:
-
P or P0 ≦ 0,05 · C0a.
- The angular deviation is constant (static angular misalignment).
- The rotating component is the shaft locating washer
Permissible skewing under static misalignment
Bearing series |
Permissible skewing |
|
---|---|---|
D < 320 mm |
D ≧ 320 mm |
|
292..-E1 |
1,5° |
1° |
293..-E1 |
2,5° |
1,5° |
294..-E1 |
3° |
2° |
D = bearing outside diameter
If the rotating component is the housing locating washer or the shaft locating washer undergoes tumbling motion, the angular adjustment facility is smaller. In such cases, please consult Schaeffler.
Lubrication
Oil lubrication is predominantly used
Axial spherical roller bearings are not greased. They are generally lubricated using oil. In some cases, lubrication with greases containing EP additives is also possible. In this instance, however, it must be ensured that the contact points between the rollers and the guidance rib are always adequately supplied with grease. This is best achieved if the bearing is completely filled with grease and regularly relubricated.
Pay attention to the pumping action in bearings with oil lubrication
Due to their internal construction, a pumping action occurs in bearings with an asymmetrical cross-section. This pumping action, which is heavily dependent on the circumferential speed, can be used under certain conditions to generate oil recirculation in the bearing ➤ Figure. The pumping action is present in bearing arrangements with a horizontal and vertical shaft and must be taken into account when selecting the lubrication and sealing method.
The volume flow generated by the bearings can easily reach a throughput of > 50 l/min. In order to give appropriate possibilities for compensation, ducts for the purposes of oil return must therefore be included in the housing ➤ Figure.
If there is any uncertainty regarding the suitability of the selected lubricant for the application, please consult Schaeffler or the lubricant manufacturer.
Oil recirculation by means of pumping action, ducts for the purposes of oil return
|
![]() |
Sealing
The bearings are of an open design; provide seals in the adjacent construction
Axial spherical roller bearings are supplied without seals. In the case of unsealed bearings, sealing of the bearing position must be carried out in the adjacent construction. The sealing system should reliably prevent:
- moisture and contaminants from entering the bearing
- the egress of lubricant from the bearing position.
Speeds
Speeds in the product tables
The achievable operating speed is dependent on the application, the associated loads and the lubrication. The product tables generally give two speeds for the bearings ➤ dimension table:
- the kinematic limiting speed nG
- the thermal speed rating nϑr
Limiting speeds
The limiting speed nG is the kinematically permissible speed of the bearing. Even under favourable mounting and operating conditions, this value should not be exceeded without prior consultation with Schaeffler ➤ link.
Reference speeds
nϑr is used to calculate nϑ
The thermal speed rating nϑr is not an application-oriented speed limit, but is a calculated ancillary value for determining the thermally safe operating speed nϑ ➤ link.
Noise
Schaeffler Noise Index
The Schaeffler Noise Index (SGI) is not yet available for this bearing type ➤ link. The data for these bearing series will be introduced and updated in stages.
Temperature range
Limiting values
The operating temperature of the bearings is limited by:
- the dimensional stability of the bearing rings and rolling elements
- the cage
- the lubricant
Possible operating temperatures of axial spherical roller bearings ➤ Table.
Permissible temperature ranges
Operating temperature |
Axial spherical roller bearings |
---|---|
|
–30 °C to +200 °C, limited by the lubricant |
In the event of anticipated temperatures which lie outside the stated values, please contact Schaeffler.
Cages
Sheet steel cages or solid brass cages are used as standard
Axial spherical roller bearings essentially differ in terms of their cage design ➤ Figure. The design is dependent on the bearing series and the bearing size ➤ Table. Sheet steel cages do not have a cage suffix in the designation ➤ Table. The cages have a high strength. They are suitable for high temperatures and all conventional lubricants.
If there is any uncertainty regarding cage suitability for a specific application, please consult Schaeffler.
Cage, cage suffix, bore code
Bearing series |
Sheet steel cage |
Solid brass cage |
---|---|---|
MB |
||
Bore code |
||
292..-E1 |
‒ |
30 to /1180 |
293..-E1-XL |
17 to 64 |
68 to /800 |
293..-E1 |
‒ |
/850 to /1600 |
294..-E1-XL |
12 to 68 |
72 to /710 |
294..-E1 |
‒ |
/750 to /1060 |
Internal clearance
The possible preload is determined by the application
In the case of axial spherical roller bearings, the axial preload is achieved when the bearings are mounted. The requisite preload is dependent on the application and must take account of the conditions in the bearing arrangement while warm from operation and subjected to load. It must always be ensured that no slippage occurs in operation between the rolling elements and raceways. A specific minimum axial load Fa min must be acting on axial spherical roller bearings at all times ➤ section.
If there is any uncertainty regarding preload, please consult Schaeffler.
Dimensions, tolerances
Dimension standards
The main dimensions of axial spherical roller bearings correspond to ISO 104:2015 and DIN 728:1991.
Chamfer dimensions
The limiting dimensions for chamfer dimensions correspond to DIN 620-6:2004. Overview and limiting values ➤ link. Nominal value of chamfer dimension ➤ dimension table.
Tolerances
The dimensional and running tolerances of shaft and housing locating washers correspond to the tolerance class Normal in accordance with ISO 199:2014 ➤ Table to ➤ Table.
Restricted section height tolerance
The tolerances for section height T are considerably restricted for all axial spherical roller bearings compared to the standard values ➤ Table and ➤ dimension table.
Tolerances for bearing section height
Nominal bore diameter |
Deviation of bearing section height T |
||
---|---|---|---|
mm |
μm |
||
over |
incl. |
upper |
lower |
50 |
80 |
0 |
–100 |
80 |
120 |
0 |
–100 |
120 |
180 |
0 |
–125 |
180 |
250 |
0 |
–125 |
250 |
315 |
0 |
–150 |
315 |
400 |
0 |
–200 |
400 |
500 |
0 |
–420 |
500 |
630 |
0 |
–500 |
630 |
800 |
0 |
–630 |
800 |
1 000 |
0 |
–800 |
1 000 |
1 250 |
0 |
–1 000 |
1 250 |
1 600 |
0 |
–1 200 |
Suffixes
For a description of the suffixes used in this chapter ➤ Table and medias interchange http://www.schaeffler.de/std/1B69.
Suffixes and corresponding descriptions
Suffix |
Description of suffix |
|
---|---|---|
E1 |
Increased capacity design |
Standard |
MB |
Solid brass cage |
|
N1 |
One retaining slot |
|
N2 |
Two retaining slots offset by 180° |
|
THI |
3 uniformly distributed threaded holes |
|
THIE |
3 uniformly distributed threaded holes |
|
THO |
3 uniformly distributed threaded holes |
|
THOE |
3 uniformly distributed threaded holes |
|
XL |
X-life bearing |
Structure of bearing designation
Examples of composition of bearing designation
The designation of bearings follows a set model. Examples ➤ Figure and ➤ Figure. The composition of designations is subject to DIN 623-1 ➤ Figure.
Axial spherical roller bearing, X-life design: designation structure |
![]() |
Axial spherical roller bearing, X-life design, with retaining slot and threaded holes: |
![]() |
Dimensioning
Equivalent dynamic bearing load
P = a substitute force for combined load and various load cases
The basic rating life equation L = (C/P)p used in the dimensioning of bearings under dynamic load assumes a load of constant magnitude and direction. In the case of axial bearings, this is a purely axial and concentrically acting load. If this condition is not met, an equivalent dynamic bearing load P must be determined for the rating life calculation. In the case of axial bearings, this is a concentrically acting axial load of constant magnitude and direction, which has the same effect on the rating life as the load occurring in practice. Calculation ➤ Equation.
Equivalent dynamic load

Legend
P | N |
Equivalent dynamic bearing load |
Fr | N |
Radial load |
Fa | N |
Axial load |
The radial bearing load Fr must not exceed 55% of the axial load Fa: Fr ≦ 0,55 · Fa
Equivalent static bearing load
For axial spherical roller bearings subjected to static load ➤ Equation.
Equivalent static load

Legend
P0 | N |
Equivalent static bearing load |
F0r, F0a | N |
Largest radial or axial load present (maximum load). |
The radial bearing load F0r must not exceed 55% of the axial load F0a: F0r ≦ 0,55 · F0a
Static load safety factor
In addition to the basic rating life L(L10h), it is also always necessary to check the static load safety factor S0. The following values must be observed here ➤ Table. Calculation of S0 ➤ Equation.
Static load safety factor
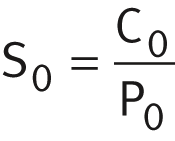
Legend
S0 |
Static load safety factor |
|
C0 | N |
Basic static load rating |
P0 | N |
Equivalent static bearing load. |
Values for static load safety factor
Static load S0 |
Conditions |
---|---|
S0 ≧ 8 |
Axial support by the abutment shoulders in accordance |
S0 ≧ 6 |
Full axial support of the housing and shaft locating washers |
S0 ≧ 4 |
Full axial support, dimensions D1 and d1 ➤ dimension table together |
Minimum load
Rolling bearings under low loads are particularly prone to slippage
If the lubricant film is interrupted between the rolling elements and raceways as a result of slippage, the contact partners will come into contact at high relative velocity and the wear in the bearing will increase abruptly. The risk of slippage is particularly high where bearings are subjected to low loads. In order to prevent slippage damage and guarantee kinematics, a minimum axial load Fa min must therefore be applied to the bearing ➤ Equation and ➤ Table.
Preload the bearings, if the minimum axial load is not achieved
In vertical bearing arrangements in particular, the requisite minimum axial load Fa min is normally already achieved by the weight of the supported parts and the external forces. If this is not the case, the bearing arrangement must be preloaded, for example by means of springs or a shaft nut ➤ Figure and ➤ section. The minimum axial load must be ensured in all operating modes.
Minimum axial load applied to an axial spherical roller bearing by means of spring preload
|
![]() |
Minimum axial load
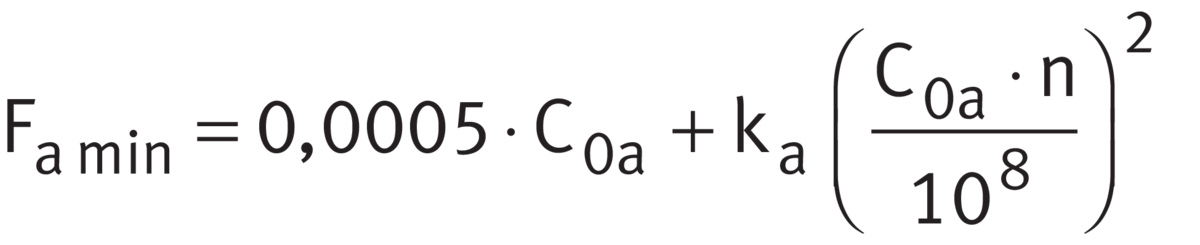
Legend
Fa min | N |
Minimum axial load |
C0a | N |
Basic static load rating ➤ dimension table |
ka |
Factor for determining the minimum load ➤ Table |
|
n | min–1 |
Speed. |
Factor ka for calculating the minimum axial load
Bearing series |
Factor ka |
---|---|
292..-E1 |
0,6 |
293..-E1 |
0,9 |
294..-E1 |
0,7 |
Design of bearing arrangements
Design of adjacent parts
Support bearing washers over the circumference and width
The adjacent parts to the shaft and housing locating washers must be rigid, flat and perpendicular to the axis of rotation. They must be configured such that the bearing washers are supported over the whole circumference and over the whole raceway width; in particular, this must be observed under high loads. The axial runout tolerances of the contact surfaces for axial spherical roller bearings should be designed to IT5 or better ➤ Table.
The housing bore must have a recess with a diameter Db min above the housing locating washer, otherwise the rollers may graze the housing in the event of shaft misalignments ➤ Figure. Dimensions for Db min ➤ dimension table.
E1 = bearings with new internal construction
Due to the new internal construction of the E1 bearings, attention must be paid to the mounting dimensions. This also applies to the configuration of the spacer sleeve on the shaft locating washer (dimensions db, db1) ➤ dimension table.
Release in the housing and maximum height of spacer sleeve Db min = minimum dimension of recess in the housing dmax = maximum height of spacer sleeve
|
![]() |
Numerical values for ISO standard tolerances (IT grades) to ISO 286-1:2010
IT grade |
Nominal dimension in mm |
||||||
---|---|---|---|---|---|---|---|
over |
50 |
80 |
120 |
180 |
250 |
315 |
|
incl. |
80 |
120 |
180 |
250 |
315 |
400 |
|
Values in μm |
|||||||
IT5 |
13 |
15 |
18 |
20 |
23 |
25 |
|
continued ▼ |
Numerical values for ISO standard tolerances (IT grades) to ISO 286-1:2010
IT grade |
Nominal dimension in mm |
||||||
---|---|---|---|---|---|---|---|
over |
400 |
500 |
630 |
800 |
1000 |
1250 |
|
incl. |
500 |
630 |
800 |
1000 |
1250 |
1600 |
|
Values in μm |
|||||||
IT5 |
27 |
32 |
36 |
40 |
47 |
55 |
|
continued ▲ |
Tolerances for shaft and housing bore
Observe point or circumferential load of bearing washers
Fits for the bearing rings of axial spherical roller bearings, as a function of the condition of rotation ➤ Table . The conditions of rotation for shaft and housing locating washers must be taken into consideration when defining the fits (point or circumferential load).
Conditions of rotation and fits
Adjacent part |
Type of load |
Operating conditions |
Tolerance class |
---|---|---|---|
Shaft |
Combined load |
Point load for shaft locating washer |
j6 |
Circumferential load for shaft locating washer, shaft diameter up to 200 mm |
j6 (k6) |
||
Circumferential load for shaft locating washer, shaft diameter from 200 mm |
k6 (m6) |
||
Housing |
Axial load |
Normal load |
E8 |
High load |
G7 |
||
Combined load |
Point load for housing locating washer |
H7 |
|
Circumferential load for housing locating washer |
K7 |
- The envelope requirement Ⓔ applies.
If there is any uncertainty regarding the design of adjacent parts, please consult Schaeffler.
Mounting and dismounting
The mounting and dismounting options for the bearings must be taken into consideration in the design of the bearing position.
The bearings are easy to mount, as they are not self‑retaining
Axial spherical roller bearings are not self-retaining. As a result, the bearing parts can be mounted separately from each other. This gives simplified mounting of the bearings.
Schaeffler Mounting Handbook
Rolling bearings must be handled with great care
Rolling bearings are well-proven precision machine elements for the design of economical and reliable bearing arrangements, which offer high operational security. In order that these products can function correctly and achieve the envisaged operating life without detrimental effect, they must be handled with care.
The Schaeffler Mounting Handbook MH 1 gives comprehensive information about the correct storage, mounting, dismounting and maintenance of rotary rolling bearings http://www.schaeffler.de/std/1B68. It also provides information which should be observed by the designer, in relation to the mounting, dismounting and maintenance of bearings, in the original design of the bearing position. This book is available from Schaeffler on request.
Legal notice regarding data freshness
The further development of products may also result in technical changes to catalogue products
Of central interest to Schaeffler is the further development and optimisation of its products and the satisfaction of its customers. In order that you, as the customer, can keep yourself optimally informed about the progress that is being made here and with regard to the current technical status of the products, we publish any product changes which differ from the printed version in our electronic product catalogue.
We therefore reserve the right to make changes to the data and illustrations in this catalogue. This catalogue reflects the status at the time of printing. More recent publications released by us (as printed or digital media) will automatically precede this catalogue if they involve the same subject. Therefore, please always use our electronic product catalogue to check whether more up-to-date information or modification notices exist for your desired product.
Further information
In addition to the data in this chapter, the following chapters in Technical principles must also be observed in the design of bearing arrangements: